Molding Quality Plastic Parts
Ensure high-quality injection molded products through material selection, precise machine parameter settings, controlled molding processes, rigorous quality inspections, and efficient automation, all implemented according to CENTERMold’s rigorous standards.
Molding Process
Our comprehensive suite of professional services caters to a diverse clientele, ranging from homeowners to commercial developers.
Material Selection and Procurement
Resin Selection: Working with clients to select the appropriate resin based on the part’s functional requirements and application.
Material Procurement: Sourcing high-quality plastic resins from trusted suppliers to ensure consistency and performance.
Pre-Processing Preparation: Drying materials in a desiccant dryer to eliminate moisture and ensure optimal material properties during molding.
Mold Setup and Preparation
Mold Installation: Carefully installing the mold into the injection molding machine, ensuring all components are properly aligned.
Machine Calibration: Calibrating the injection molding machine settings to match the specific requirements of the mold and material.
Hot Runner Systems: For molds with hot runner systems, ensuring that the temperature settings are optimized for efficient material flow and minimal waste.
Injection Molding Machine Preparation
Purging: Thoroughly purging the injection molding machine to eliminate any residual material and prevent contamination, ensuring the highest quality output.
Parameter Setup: Precisely setting up machine parameters, including temperature, pressure, and cycle time, to ensure consistent product quality.
Automated Handling: Employing automated robotic arms to enhance efficiency and prevent workplace injuries, ensuring safe and precise handling of molded parts.
Production and Quality Control and Inspection
In-Process Monitoring: Conducting real-time monitoring and adjustments during the molding process to maintain consistent quality.
Dimensional Inspection: Using precision measuring tools to verify that the molded parts meet dimensional specifications.
Surface Finish Inspection: Checking for surface defects and ensuring the parts meet aesthetic and functional requirements.
Functional Testing: Conducting tests to ensure the parts meet the required functional and performance standards.
Secondary Operations
Post-Molding Treatments: Performing additional treatments such as annealing, coating, or assembly as required by the client.
Finishing: Conducting trimming, deburring, and other finishing operations to prepare the parts for use.
Insert Installation: If not already done during molding, installing inserts such as threaded nuts, bushings, or other components.
Packaging and Delivery
Protective Packaging: Ensuring molded parts are securely packaged to prevent damage during transportation.
Custom Packaging Solutions: Providing packaging solutions tailored to the specific requirements of the parts, including anti-static bags, custom boxes, and protective wraps.
Logistics Coordination: Coordinating with trusted logistics partners to ensure timely and safe delivery to the client’s location.
Molding Parts Sample
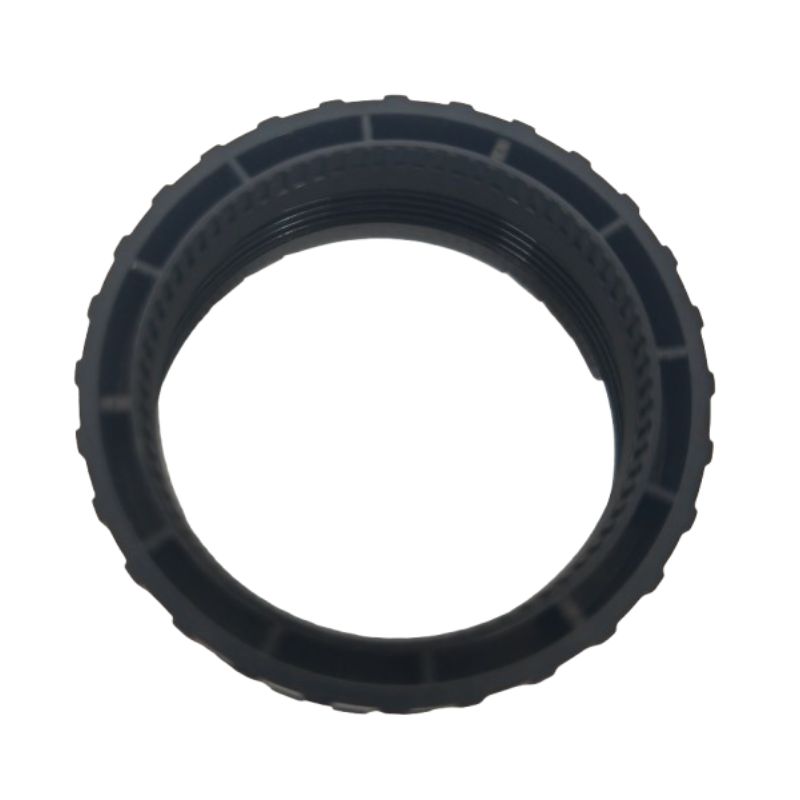
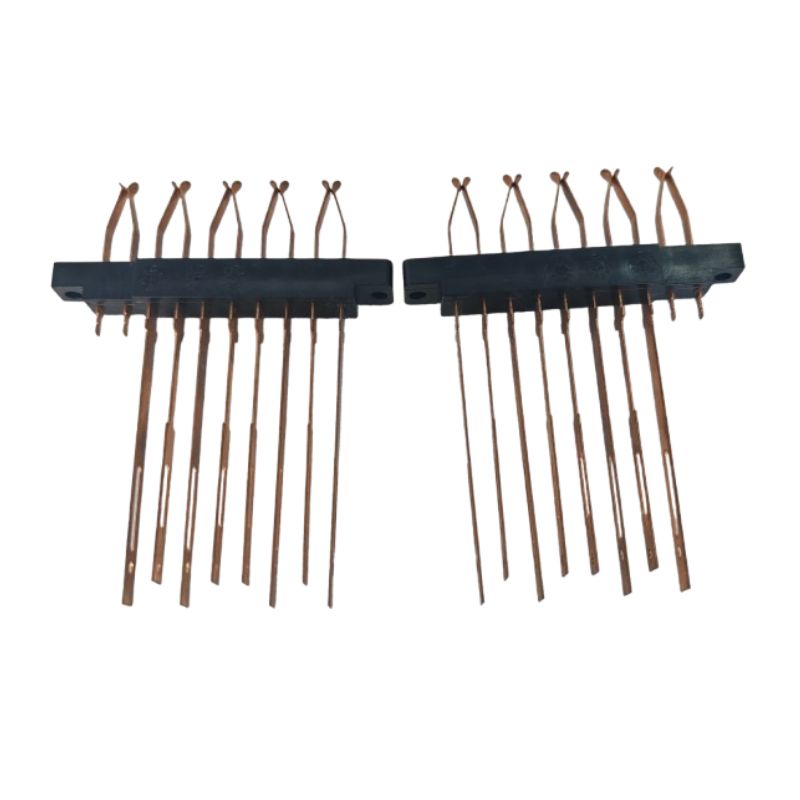

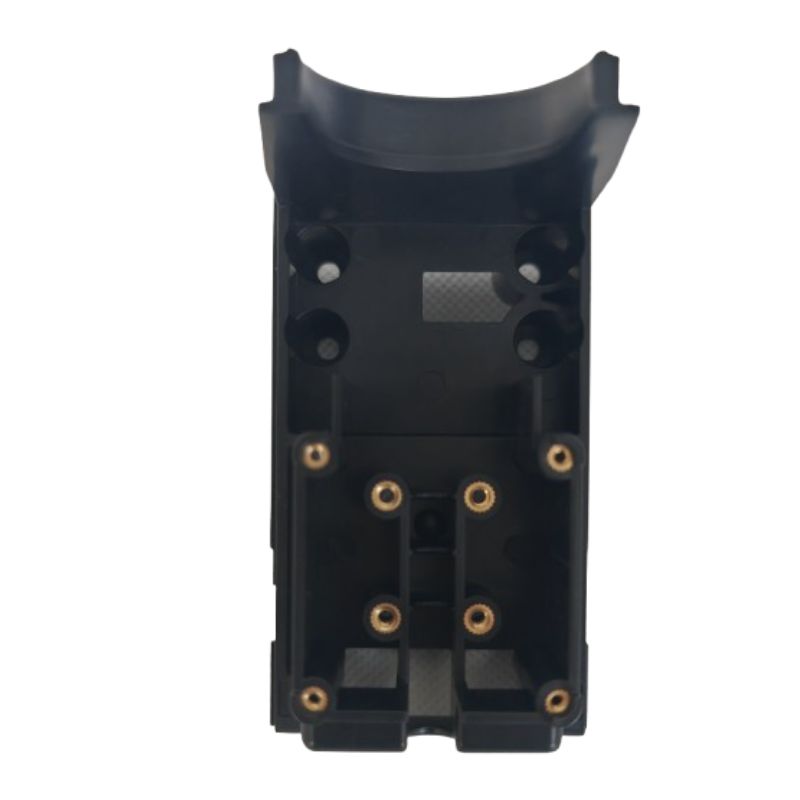
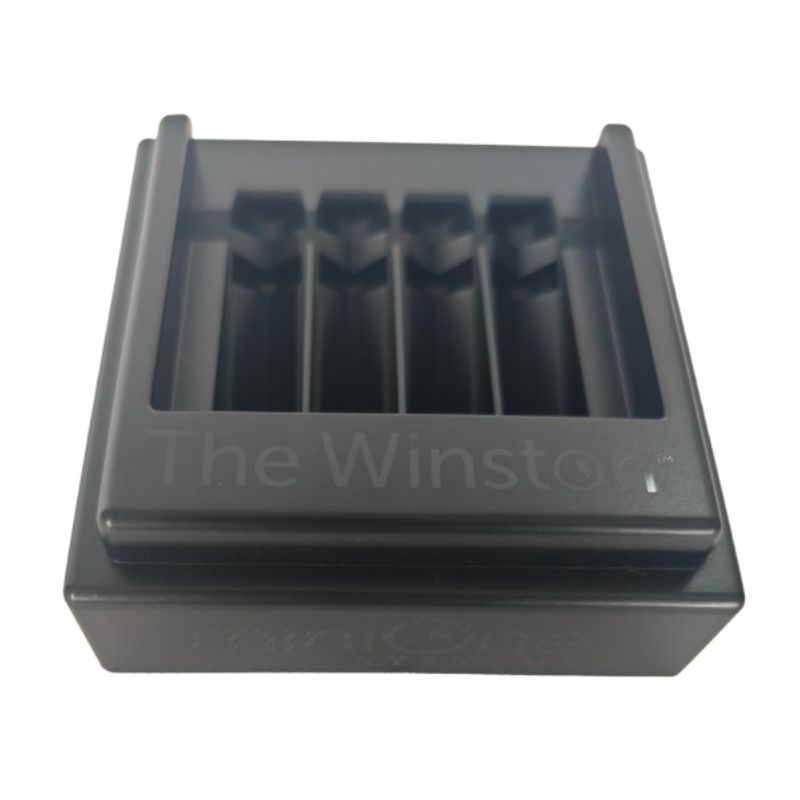
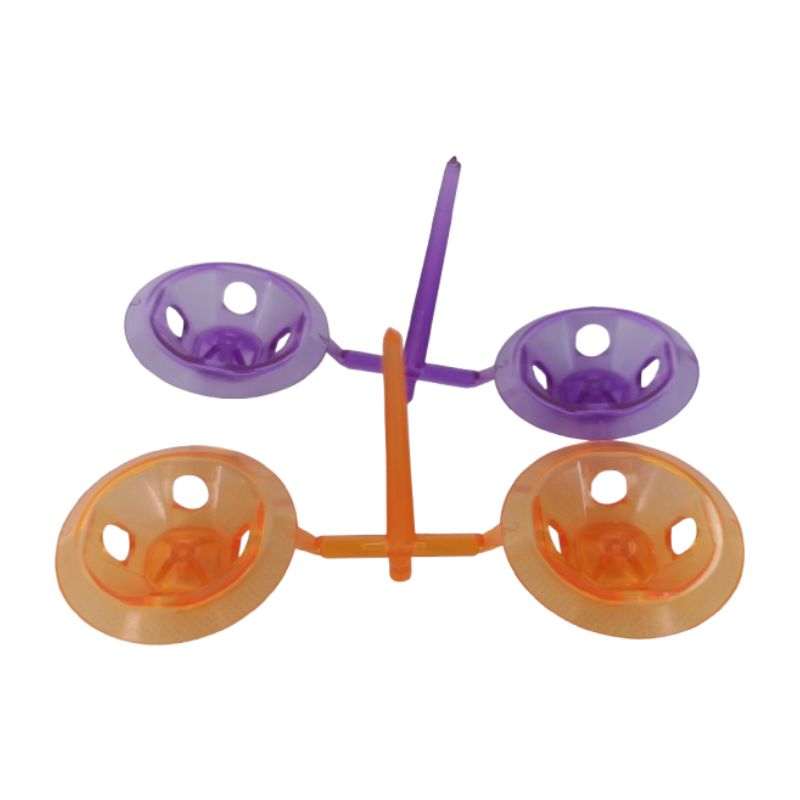
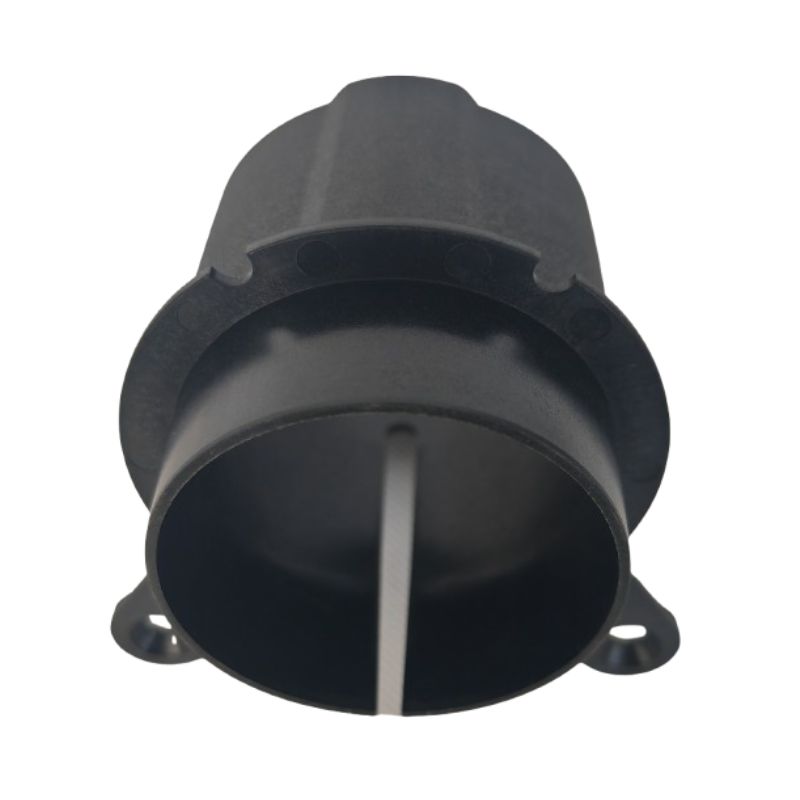
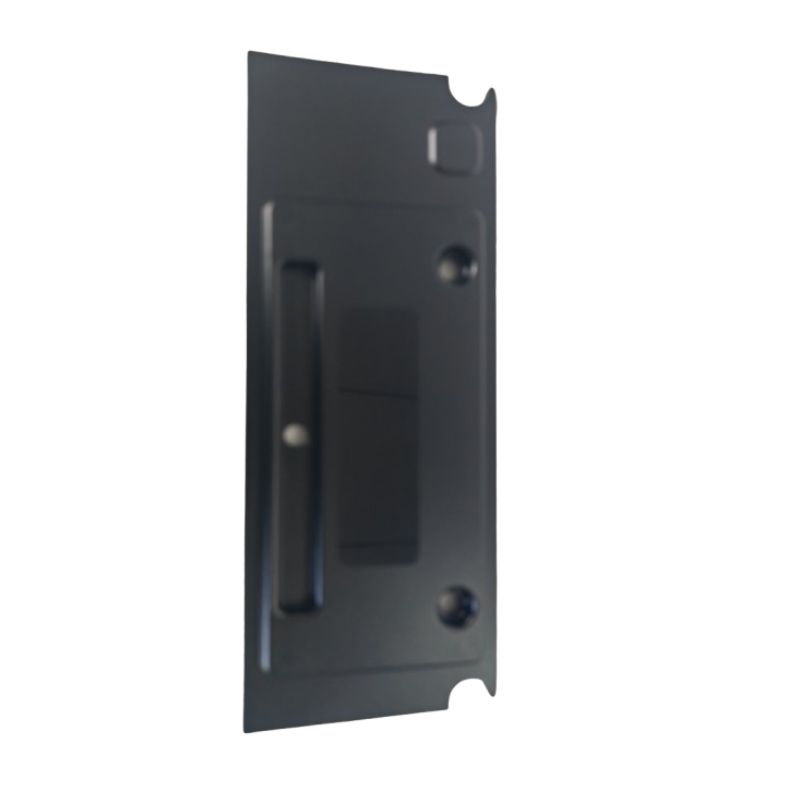
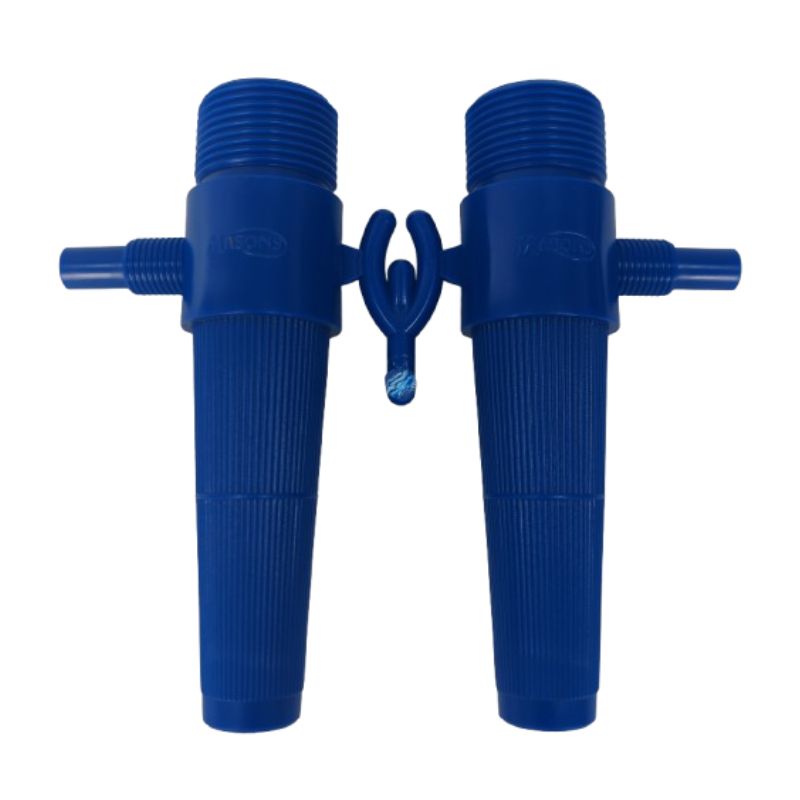